PDM IN THE INDUSTRY 4.0 ENVIRONMENT: TOWARDS INTELLIGENT PREDICTION
IN THE PAST, WE HAVE ARGUED THAT RELIABILITY-BASED INDUSTRIAL MAINTENANCE ALLOWS US TO OPTIMISE OUR STRATEGY.
IN THIS ARTICLE WE WILL UNPACK THE POTENTIAL OF IOT TO TAKE PREDICTIVE MAINTENANCE TO A NEW STAGE.
Written by Marketing
4 Dec 2020 | Predictive | Article
That reliability allows us to optimise our strategy is not a statement just thrown out there.
In the 30 years that predictive maintenance has been in force in our industry, companies that have opted for it have managed to gain competitiveness.
Predictive maintenance makes it possible to increase the useful life of assets, avoid production stoppages and reduce annual interventions. But it also improves product quality, avoids polluting emissions and discharges, and increases plant safety.
But... What is the road to intelligent predictive?
Despite all these certainties, the implementation of predictive maintenance in industry has not been easy. Either because of a lack of investment capacity or because of a lack of support from company management.
But the truth is that, in an increasingly globalised and competitive environment, companies that do not pursue operational excellence run a significant risk of disappearing.
In this sense, Industry 4.0 offers companies an opportunity, perhaps the last one, to achieve this excellence.
Never before have we had such a wealth of technology at our fingertips to drive a change of model.
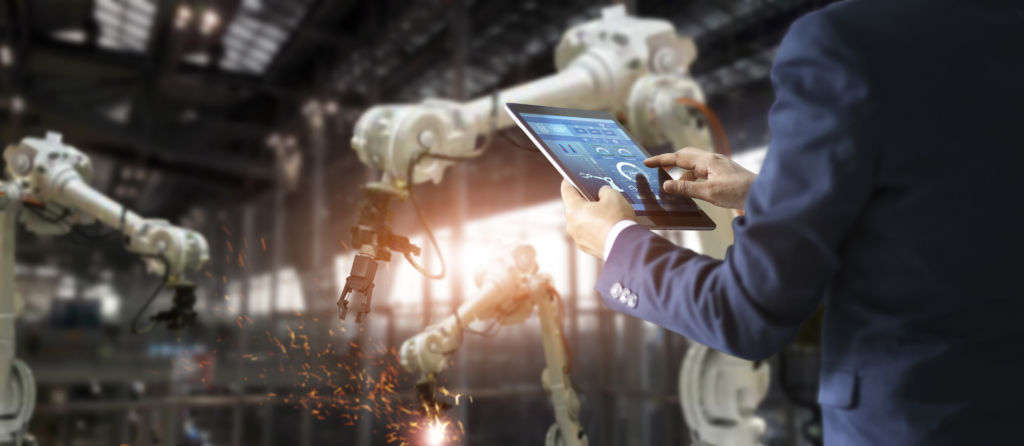
WHAT IS IOT?
To understand why industry is evolving around the Internet of Things, we must start by asking what it is. Kevin Ashton, a technologist specialising in digital transformation who coined the term, defined it as follows:
"If we had computers that knew everything there was to know about things-using data they gathered without any help from us-we would be able to track and count everything, and greatly reduce waste, loss and cost. We would know when things needed replacing, repairing or recalling, and whether they were fresh or past their best."
In general terms, we could say that the IoT allows us to monitor physical objects through sensors and devices connected to the internet.
This monitoring gives us a better understanding of our processes and allows us to optimise them, making decisions aimed at increasing productivity and making the business more profitable.
Many companies are currently working to harness the potential of new enabling technologies and turn their facilities into smart factories.
But what is a smart factory? It is a facility that has technology that allows communication between machines (M2M) and between machines and people (M2H). This constant communication has a clear objective: real-time decision making based on data.
When we apply this scheme to industrial environments, we speak of the Industrial Internet of Things (IIoT). And its enormous potential makes it the spearhead of most of the digital transformation projects.
INTELLIGENT PREDICTIVE
One of the new frontiers being drawn is that of intelligent predictive maintenance, which consists of applying this potential to predictive maintenance strategies.
The use of new technologies such as IIoT platforms allows the storage of large volumes of data and a great capacity for analysis and processing. This allows us, firstly, to manage the data obtained by all these installed sensors in a faster and more efficient way.
This data can be modelled or tested in different ways in order to identify problems in a more understandable way. It also allows us to manage alarms, plan interventions or study the root cause of failures.
Ultimately, intelligent predictive will help us to make business decisions in a more agile and accurate way.
BUT HOW DID WE GET THERE?
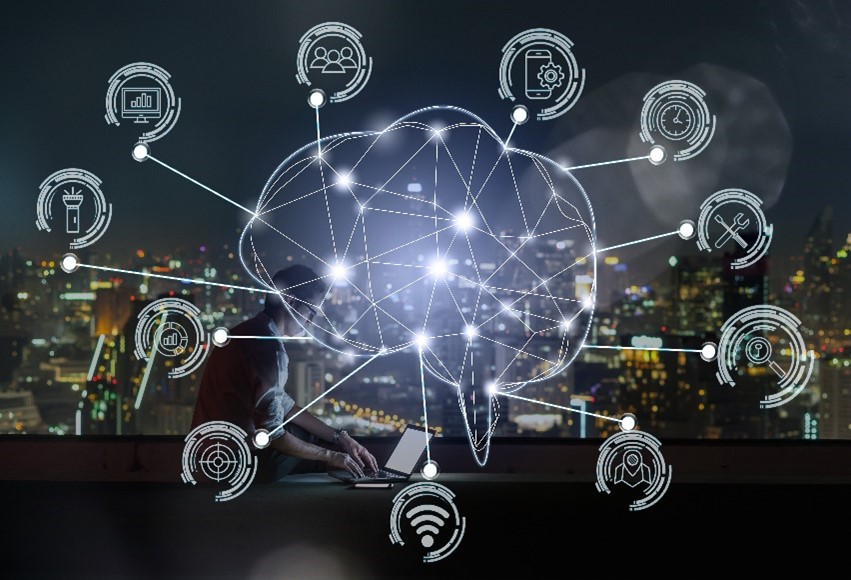
First, the platform collects and sorts all this data to compare it with the historical data stored for each device. The next step is to analyse the variations that may exist through a control panel. This analysis is possible thanks to the application of machine learning algorithms known as Machine Learning.
These algorithms identify abnormal patterns in the historical data and create predictive models capable of foreseeing new failures.
From these data patterns, predictive models are created to identify the operating conditions and use of the machines.
The next step is to attribute to these models a series of parameters that establish the levels of security and risk. That is to say, to delimit from which values the reliability of the assets is outside its optimum level.
Thus, when the platform identifies abnormal parameters, it is capable of generating automatic alarms, recommending maintenance actions and scheduling interventions at the optimum time. In addition, all this analysis capability allows for better identification of the root cause of different types of failures.
And here, the accumulated experience of a plant's maintenance technicians is crucial. Their knowledge is crucial in determining these parameters and establishing the necessary actions for the different types of failure of each machine.
This is a clear example of how people play an important role in Industry 4.0. How we can turn knowledge into tools for data-driven management and decision-making.
THE CHALLENGES POSED BY IIOT TO COMPANIES...
Do you want to read more?
More info on the challenges to be faced by companies, the return by accessing the full article in pdf format!
Fill in the form and we'll send it to you by email 🙂