PDM EN EL ENTORNO DE LA INDUSTRIA 4.0: HACIA UN PREDICTIVO INTELIGENTE
ANTERIORMENTE, HEMOS SOSTENIDO QUE UN MANTENIMIENTO INDUSTRIAL BASADO EN LA FIABILIDAD PERMITE OPTIMIZAR NUESTRA ESTRATEGIA.
EN ESTE ARTÍCULO DESGRANAREMOS EL POTENCIAL QUE TIENE EL IOT PARA LLEVAR AL MANTENIMIENTO PREDICTIVO A UN NUEVO ESTADIO.
Escrito por Marketing
4 Dic 2020 | Predictivo | Artículo
Que la fiabilidad permite optimizar nuestra estrategia no es una afirmación lanzada al aire sin más.
En los 30 años que el mantenimiento predictivo lleva vigente en nuestra industria, las empresas que han apostado por él han conseguido ganar competitividad.
El predictivo permite aumentar la vida útil de los activos, evitar las paradas productivas y reducir las intervenciones anuales. Pero también mejorar la calidad de los productos, evitar emisiones y vertidos contaminantes, o aumentar la seguridad de la planta.
Pero… ¿Cómo es el camino hacia un predictivo inteligente?
A pesar de todas estas certezas, la implantación del mantenimiento predictivo en la industria no ha sido fácil. Bien por la falta de capacidad de inversión o por la falta de apoyo de la dirección de las compañías.
Pero lo cierto es que, en un entorno cada vez más globalizado y competitivo, las compañías que no persigan la excelencia operacional corren un importante riesgo de desaparecer.
En este sentido, la Industria 4.0 ofrece a las empresas una oportunidad, quizás la última, para conseguir esta excelencia.
Nunca antes habíamos tenido a nuestro alcance tal cantidad de tecnología para impulsar un cambio de modelo.
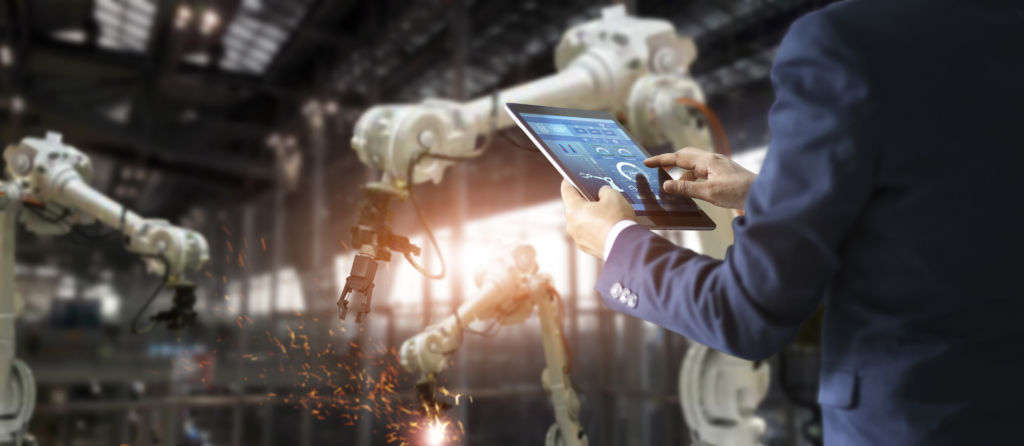
¿QUÉ ES EL IOT?
Para entender por qué la industria está evolucionando en torno al Internet de las Cosas, debemos empezar por preguntarnos qué es. Kevin Ashton, un tecnólogo especializado en transformación digital que acuñó su término, lo definió de la siguiente manera:
“If we had computers that knew everything there was to know about things—using data they gathered without any help from us—we would be able to track and count everything, and greatly reduce waste, loss and cost. We would know when things needed replacing, repairing or recalling, and whether they were fresh or past their best.”
En líneas generales, podríamos decir que el IoT permite monitorizar objetos físicos a través de sensores y dispositivos conectados a internet.
Esta monitorización nos permite conocer mejor nuestros procesos y permite optimizarlos, tomando decisiones encaminadas a aumentar la productividad y rentabilizar el negocio.
Son muchas las empresas que están actualmente trabajando para aprovecharse del potencial de las nuevas tecnologías habilitadoras y convertir sus instalaciones en fábricas inteligentes.
Pero ¿qué es una fábrica inteligente? Es aquella instalación que dispone de tecnología que permite la comunicación entre máquinas (M2M) y entre máquinas y personas (M2H). Esta comunicación constate tiene un objetivo claro: la toma de decisiones en tiempo real basada en datos.
Cuando aplicamos este esquema a entornos industriales, hablamos de Industrial Internet of Things (IIoT). Y su enorme potencial lo convierten en la punta de lanza de la mayor parte de los proyectos de transformación digital.
EL PREDICTIVO INTELIGENTE
Una de las nuevas fronteras que se dibujan es la del predictivo inteligente, que consiste en aplicar este potencial a las estrategias de mantenimiento predictivo.
El uso de nuevas tecnologías como las plataformas IIoT permiten el almacenamiento de grandes volúmenes de datos y una gran capacidad de análisis y procesamiento. Esto nos permite, en primer lugar, gestionar los datos obtenidos por todos estos sensores instalados de una manera más rápida y eficiente.
Estos datos pueden ser modelados o probados de diferentes maneras para lograr identificar los problemas de una manera más comprensible. También nos permite gestionar alarmas, planificar intervenciones o estudiar la causa raíz de los fallos.
En definitiva, el predictivo inteligente nos ayudará a tomar decisiones de negocio de una manera más ágil y certera.
PERO ¿CÓMO LLEGAMOS HASTA AHÍ?
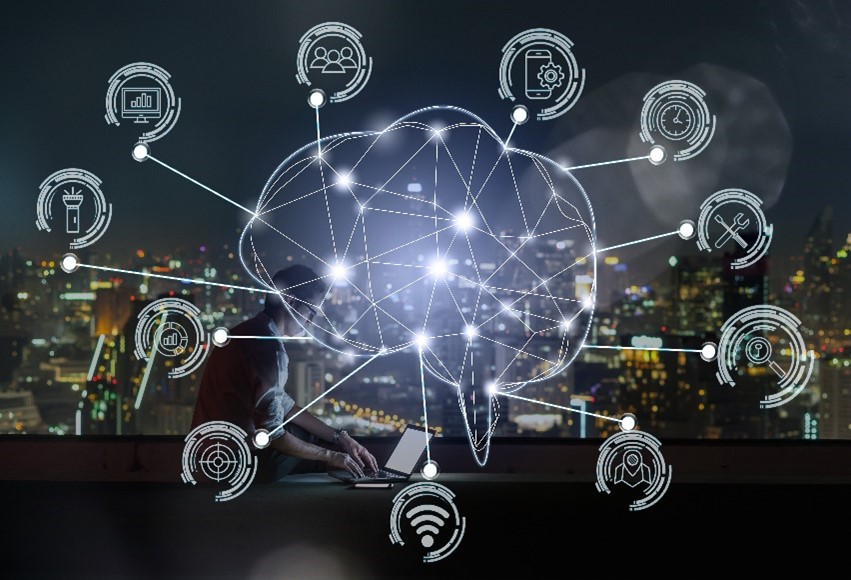
En primer lugar, la plataforma recopila y ordena todos estos datos para compararlos con el histórico de datos almacenado de cada equipo. El siguiente paso, es analizar las variaciones que puedan existir a través de un panel de control. Este análisis es posible gracias a la aplicación de algoritmos de aprendizaje automático, conocido como Machine Learning.
Estos algoritmos identifican en el histórico de datos patrones anormales y crean modelos predictivos capaces de prever nuevos fallos.
A partir de estos patrones de datos se crean modelos predictivos para identificar las condiciones de funcionamiento y uso de las máquinas.
El siguiente paso es atribuir a estos modelos una serie de parámetros que establezcan los niveles de seguridad y de riesgo. Es decir, delimitar a partir de qué valores la fiabilidad de los activos está fuera de su nivel óptimo.
Así, cuando la plataforma identifica parámetros anormales es capaz de generar alarmas automáticas, recomendar acciones de mantenimiento y programar intervenciones en el momento óptimo. Además, toda esta capacidad de análisis permite puertas a mejorar la identificación de la causa raíz de los diferentes tipos de fallo.
Y en este punto, es crucial la experiencia acumulada de los técnicos de mantenimiento de una planta. Su conocimiento es crucial a la hora de determinar estos parámetros y establecer las acciones necesarias para los diferentes tipos de fallo de cada máquina.
Este es un claro ejemplo de cómo las personas juegan un importante papel en la Industria 4.0. Cómo podemos convertir el conocimiento en herramientas para la gestión y la toma de decisiones basadas en datos.
LOS DESAFÍOS QUE PLANTEA EL IIOT A LAS EMPRESAS…
¿Quieres seguir leyendo?
Más info sobre los desafíos a afrontar por las empresas, el retorno accediendo al artículo completo en formato pdf!
Completa el formulario y te lo enviaremos por email 🙂